The market for electrical vehicles (EVs) and the battery cells that power them is growing fast, with companies the world over competing to take a share of this lucrative opportunity.
The driving force behind this momentum was sparked by global commitments and pressures to reduce carbon emissions to net zero by 2050. This means higher taxes and stricter regulations on fossil fuel cars, plus onerous requirements on manufacturers to meet electric vehicle (EV) quotas.
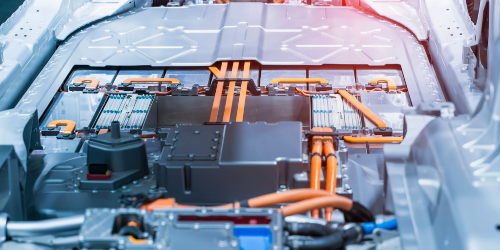
Supercharged financial projections
In 2020 the global EV market was valued at $163.01 billion and it’s projected to reach $823.75 billion by 2030. It’s a fiercely contested industry that’s dominated by Asian companies - with China currently producing some 80% of the world’s lithium-ion battery cells.
All of the top 10 EV battery manufacturers by market share have headquarters across Asia, primarily within China, Japan, and South Korea. But how did Asia get so far ahead? One popular theory is that the European automotive giants weren’t fast enough to recognise and position for the opportunity. But factors such as EV favourable government policies in China and direct access to in-country mining resources surely play a part.
The trials of the pandemic world demonstrated the dangers of over-reliance on one geography for supply of products and materials. With lockdowns imposed and supply chains disrupted, vital resources became harder to move across borders, sometimes even hoarded within the country of origin.
Some parts of the world, including Russia and Australia, are lagging behind in the race for battery independence. But across Europe and North America, all sorts of companies have recognised the financial opportunity and the potential pitfalls of inaction. They’re now exploiting the investment initiatives and government subsidies on offer to plan some ambitious and innovative projects.
At Coalesce Management Consulting (CMC) we supply talented consultants to plan and deliver many of these projects. As a strategic capacity partner for several companies we help to identify any gaps in their capacity to develop EV battery projects and the associated mining facilities. We then fill these gaps with the best people, for as long as the skills are needed.
Europe: the electrified race is on
Fernando Bellod, the Hague-based Business Development Manager for CMC, is particularly excited about the growth rate potential in Europe. He said: “Europe is the fastest growing region for lithium iron battery capacity outside of China. The European battery market is expected to grow at a CAGR of 7.15% - from $14.5 billion in 2020 to $23 billion in 2027.
“Just three years ago experts predicted that Europe’s annual battery cell capacity would reach 120GW by 2030 - enough to power 2.2m electrical vehicles. But a recently updated projection is more aspirational, with expected annual capacity now at 800GWh - a six-fold increase and enough to produce almost 15 million EVs by the end of the decade!”
Major Asian players such as CATL Ltd, Samsung, Panasonic and LG are already investing in opportunities across the continent, but home grown companies are quickening and catalysing their efforts to catch-up. Legacy automotive manufacturers and mining companies are coming together in exciting new ventures with startups and technology specialists. Multi-stakeholder collaborations established to build three key three pillars for success: extraction and control of raw materials such as lithium and cobalt; investment in research and development; and the production of the battery cells themselves.
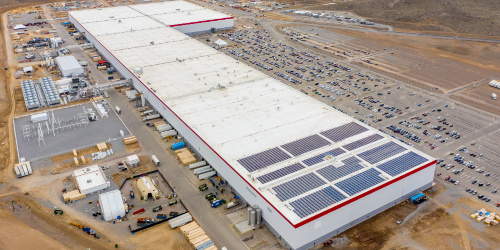
Battery powered pretenders to the throne
Fernando went on to describe some of these home-grown companies that are investing in Europe. “As early as next year, British start-up ‘Britishvolt’ is set to open the doors to the UK’s first and largest gigafactory in Northumberland, with a capacity of 35 GWh per annum,” he said. “Meanwhile, the likes of Nortvolt - a venture supported by both the Swedish government and Volkswagen and led by former Tesla executives - has plans for battery producing gigafactories across Europe as well as advanced lithium conversion units and specialised R&D campuses.”
“What exactly is a gigafactory? It’s a Tesla-coined term that relates to super-sized battery plants. There are plans to build over a dozen such facilities across Europe in the coming years in countries including Great Britain, France, Germany, Sweden, Norway, Poland, Slovakia and Hungary.”
But by the end of the decade, it’s hoped that Europe will have around 30 gigafactories, creating a production capacity that will break China’s current near-monopoly and reduce dependency on Asian imports. Indeed, Europe is aiming for a 25% share of the global battery manufacturing business by 2030, up from around six percent today.
A commodities-driven market
The technology of the lithium battery itself and the price you pay for it, is fairly comparable in any part of the world. It’s the price of the essential commodities needed to build the battery that drives the price of production and the final cost to the consumer.
This year we’ve seen the cost of production soar, with lithium prices leaping 118 per cent since January and cobalt, aluminium and nickel all enjoying historic rallies. This has been sparked by Russia versus Ukraine induced supply chain disruption fears, coupled with rebounding post-pandemic demand across developed economies.
Alarmingly, at projected rates, experts have warned that we have as little as 20 years of availability for some of the essential natural resources needed. And it’s not just a future dilemma: we’ve already seen some nickel deficits of late, while shortfalls of up to 50% in copper, cobalt, graphite and lithium are forecast for the next couple of years.
Fortunately a number of innovative start-ups are emerging in a niche market to develop solutions to counteract the raw material shortages. They’re refining powdered lithium to optimise efficiency or researching ways to recover more cobalt, graphite, copper and nickel particles from tailings or waste ponds for reuse.
Opportunities and market growth in battery production
Before worrying too much about future resource shortfalls, Fernando explained that his clients are facing a more pressing people-shaped problem.
He said: “There will be tens, if not hundreds of thousands of jobs required in the industries connected to battery production in the coming years. Lots of highly skilled people are needed to drive this electrified future…all at once! And the vital skills are facing fierce competition across multiple industries.
“They need teams of civil engineers for major construction sites, they want chemical process engineers and mining experienced mineral and metalory specialists. And they are crying out for automation engineers with smart factory or chemical factory experience.”
Then there are geographical challenges: sometimes you simply need talent in the regions in which there might not be a lot of talent! The scarcity of a particular skill set, or a lack of linguistic diversity is another stumbling block for projects in some countries.
The CMC solution
Fortunately, while the projects are new and it’s difficult to find people with battery plant experience, the skills themselves are not. Fernando and his team work with the best international consultants who bring transferable skills and experience in smart factories, oil and gas refineries and both brown and greenfield construction sites.
Some of the companies involved are big in ambition but remain small in stature. They don’t have the budget to take on too many people for the duration of a battery plant design and build. Many aren’t traditional developers, they’re start-ups with minimal knowledge of the skills needed and when they’re required.
Fernando continued: “At CMC we offer experts from all angles of a project, layering skills that compliment each other to create a complete team that’s built for success. We speak with CEO’s to get exposure to what is happening internationally and we work with project directors and project managers at a regional level. We’re the type of company that thrives on urgency and ‘to the wire’ requirements, but you’ll feel the full benefits of our service by bringing us on board from the earliest stages of project planning.
“As a capacity strategy partner we will help you to analyse the skills you already have in-house and prepare for peaks in capacity. What permanent skills do you desperately need in the team right now? What type of people will you need on a time and materials basis and how long will you need them for?”
He explained that CMC has spent months, or even years, tracking the key projects in the EV battery market while talking to the movers and shakers involved. Simultaneously preparing teams of highly skilled consultants, ready to hit the ground running.
Based on a company’s clearly defined needs, Fernando and team line up a hypothetical team of the best consultants for the life of the project. He calls this process ‘virtual team modelling’ and it’s a useful tool to help you predict and control your costs and avoid challenging skills shortages.
He continued: “We deliver high-value consulting services and solutions across the STEM specialisms of energy, life sciences and advanced engineering. Our truly ‘bespoke’, project and relationship-led approach means we will hit your requirements in the shortest amount of time. So you will maximise your return on investment, achieve your goals and unlock the full potential of your business.”
Get in touch with Fernando today, or
contact our associates directly, to talk through how we can best support your EV battery project and solve your people-shaped business pressures.
Fernando Bellod
Direct Dial: +31 (0) 20 36 94 550 I Office: +31 (0) 20 80 80 888 | Mobile: +31 6 38 72 0911
fernando.bellod@cmc-global.consulting
Coalesce Management Consulting - true expertise delivered.